Regular Surveillance
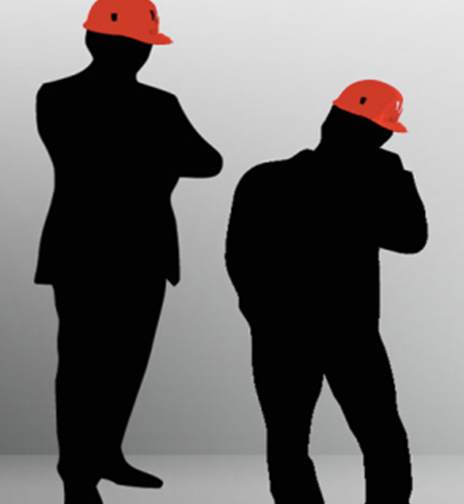
The aim of business health and safety is to protect employees' body integrity and health. Regular environmental monitoring is the identification of health and safety risks in the workplace and all protective, preventive and corrective actions to be taken against those risks. Dangers and risks in the work environment are constantly changing. The new ramak causes strikes, job accidents and occupational diseases.
Is Occupational Surveillance an Obligation for OHS?
The obligation to supervise the working environment of employers is included in the Law on Occupational Health and Safety No. 6331, published by the Official Gazette dated June 30, 2012 and numbered 28339, and the various regulations issued pursuant to this law.
According to the Law No. 6331 on Occupational Health and Safety; 'The employer who is obliged to take all kinds of precautions in order to ensure occupational health and safety in the workplace must establish a system for the supervision of the work environment and record the structures in order to determine that he fulfills this and the obligation to supervise.'
The working environment may fulfill its obligation by appointment of the employer from among his or her staff, or by receiving services from the firm established outside the workplace.
There are various provisions in our occupational health and safety legislation regarding working environment surveillance. In this respect, occupational health and safety departments, occupational health and safety departments, workplace physicians and occupational safety specialists have duties and responsibilities.
How to Surveillance?
When the environment is monitored, the hazards and risks in the workplace are identified, a risk assessment is made, and a plan for environmental monitoring is established according to the risk assessment. The proposed proposals are presented to the employer. Corrective-preventive actions related to recommendations are followed.
When working environment supervision is being done; workplace buildings and attachments, work equipment in the workplace, materials used and produced in the workplace are taken into consideration.
What does the work environment cover?
To plan and implement periodic maintenance, control and measurements that must be done in the workplace in terms of occupational health and safety
To conduct legislative studies and follow up applications for prevention of accidents, fires or explosions at work
To prepare emergency plans for situations such as natural disaster, accident, fire or explosion
Having trainings and exercises periodically
Ensuring that the movement is in line with the emergency plan
When workplace ambient surveillance is being carried out, the structure of the buildings, the height of the ceiling, the electrical installation (conformity with the Electrical Internal Installation Regulations), the emergency exit routes available at the workplace, ventilation, ambient temperature, lighting, workplace base, wall, showers, toilets, first aid rooms are considered.
Legal Basis: Regulation on the Health and Safety Measures to be Taken in Workplace Buildings and Attachments, Official Gazette Date: 17.07.2013 / 28710
Work equipment is taken into account when measuring the workplace environment. Appropriate precautions shall be taken to minimize the risk if the machine, equipment and facilities used in the work are not completely safe and the specific working conditions in the workplace are to be taken into account in consideration of health and safety. M work equipment in the workplace is taken into account when supervision is carried out.
Legal Basis: Regulation on Health and Safety Conditions in the Use of Work Equipment, Official Gazette Date: 25.04.2013 Number: 28628
All work equipment must have a system that will stop the equipment completely and safely.
Appropriate protective measures should be taken against the risk of breakage, breakage or disintegration of parts of work equipment. The moving parts of the work equipment must be housed in suitable, sturdy protectors. Warning signs of the work equipment must be easily detected. Maintenance work should be done when the equipment is switched off. Maintenance-related operations must be recorded on the day of the day.
When working environment supervision is carried out, materials used and produced in the workplace are taken into consideration. Material safety documents (MSDS) are not used during storage and production of materials. Precautions should be taken according to their being flammable, explosive and toxic. The oxidizer and burners must be stored separately. It must be in accordance with the specifications of the fire-fighting equipment. Most importantly, media measurements should be made periodically. The working environment health surveillance is done by the workplace physician. When regular environment measurements are made at workplaces, workers are protected from work accidents and occupational diseases.